Automotive manufacturers around the world are transitioning their operations and opening new facilities to ramp up production of electric vehicles (EV). Due to this increased production, EV battery manufacturing will also need to be done quickly and accurately.
Though EV production is often associated with advanced technologies, machining also plays a critical role in EV manufacturing, particularly for components related to battery cells. Precision machining and metal-cutting tooling are both necessary to produce high-performance battery cell components, including housing for the batteries.
Commonly, the housing apparatus is made of an aluminum frame with thin wall construction. To effectively machine this component, manufacturers work to incorporate the latest machining technologies. Some are even developing technologies designed specifically for manufacturing electric vehicle components.
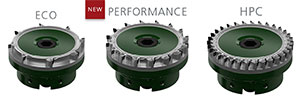
CERATIZIT HPC 3D printed face mills offer controlled chip breaking and a material removal rate of up to 60% higher than competitor face mills.
“The key is to be able to machine this component quickly, you have to be as effective in your machining time as possible,” says Mark Blosser, Executive Director of Technology and Solutions at CERATIZIT, a manufacturer of cutting tools and other material solutions.
In pursuit of this goal, CERATIZIT has employed new technologies and techniques to help manufacturers effectively machine EV components. This includes the latest metal 3D printing technology and the development of cutting tool technology with diamond cutting edges.
“We 3D print the insert mounting surface, allowing us to increase the amount of cutting edges without the limitation of normal manufacturing techniques. 3D printing also enables us to use creative geometries and improve density to be more effective with our machining times,” explains Blosser. 3D printing allows CERATIZIT to reduce the weight of tooling components without sacrificing strength, enabling greater RPM, and leading to faster machining times.
However, running at a high metal removal rate has challenges. Machinists must be careful how much tool pressure is put on certain components with thin outer walls. Too much pressure will cause deformities in the component.
There are also other challenges in designing machining tools for EV production. Tooling manufacturers need to be able to create a tool that can effectively cut dry, as many of the battery trays are weldments and it’s a problem to have coolant residue on the surface. Many of the tools will be designed for complete dry machining.
To resolve this, CERATIZIT has designed creative chip control cutting edges and fluting for swarf evacuation under the limitations of complete dry machining. Blosser elaborates: “We've used laser chip breaker designs as well as 3D printed tooling body elements to aid in chip removal.”
Manufacturers are leveraging CERATIZIT’s innovative tools for machining and milling the aluminum components for EV battery housings. Other technologies developed by CERATIZIT to more effectively machine EV components include an actuating tool that can put four effective cuts into a part, and roughing tools with internal dampeners that reduce the vibration of cutting elements for the main stator bore operations.
Some tools are designed just to reduce cycle time, while others allow for the machining of multiple features with one tool. Other tool technologies, such as programable actuating tooling and auto compensation boring heads, help to improve precision machining. These smart tools give machines more control over the cutting edges for increased accuracy of bore size and location.
“You have to design large tools at a reduced weight and take tool pressure into account to avoid deformation while also maintaining accuracy and repeatability with the tool. Those are the big challenges with creating parts to machine EV components,” explains Blosser. “The key is to figure out how to machine these large components as quickly as possible. When the market transitions to 100% e-mobility, automotive manufacturers will need EV battery and stator components for all those vehicles. Whoever can machine those parts most effectively will win in the EV market.”
CERATIZIT specializes in cutting tools and hard material solutions, and you can meet with representatives from their company, as well as other tooling suppliers, at SOUTHTEC!
Bio:
Mark Blosser, Executive Director of Technology and Solutions
Mark Blosser has held a variety of technical and leadership positions during his almost 40 years in manufacturing. He steadily built a career starting at KOMET as a Sales Engineer, before becoming Regional Manager, Director of Solution Business, VP of Engineering and Applications, and Detroit Operations Manager. In his current position as CERATIZIT’s Executive Director of Technology and Solutions, Sales and Applications, supporting the automotive industry, Mark oversees high level, complex projects that help customers optimize and streamline their operations. He holds a Computer Science degree from St. Petersburg College and a Machine Tool Technology degree from Pinellas Technical College.